Discover Reliable Packaging Equipment Repair Services for Your Organization Requirements
Specialist Solutions for Streamlined Product Packaging Tools Maintenance and Repair Providers
Expert services that use predictive upkeep techniques and take advantage of IoT modern technology provide a path to minimize unforeseen downtime and reduce expenses. As organizations look for to elevate their operational performance, one should take into consideration exactly how these ingenious techniques can change maintenance practices.
Predictive Maintenance Strategies
In the world of packaging tools upkeep, predictive upkeep techniques have actually emerged as a transformative approach to lessening downtime and enhancing operational effectiveness. Predictive maintenance relies on condition-monitoring tools and IoT-enabled sensing units that continually analyze the functional state of equipment.
The implementation of anticipating upkeep supplies several advantages. It makes it possible for companies to shift from responsive to proactive upkeep techniques, reducing the regularity and intensity of tools failings. This method not just extends the life-span of equipment but also maximizes the scheduling of upkeep tasks, guaranteeing that sources are made use of effectively and successfully. Anticipating upkeep adds to set you back savings by reducing the demand for emergency fixings and reducing manufacturing interruptions.
Tactically, firms that adopt predictive maintenance obtain an one-upmanship by enhancing tools reliability and overall performance. As technology continues to advance, the assimilation of predictive maintenance techniques right into product packaging equipment maintenance programs will increasingly become a typical technique, driving sustainable operational improvements.
Effective Repair Work Procedures
Enhancing the repair work procedure is critical for preserving the operational efficiency of product packaging devices. These guidelines need to be easily available to upkeep employees and on a regular basis updated to include the most current technological innovations and sector criteria.
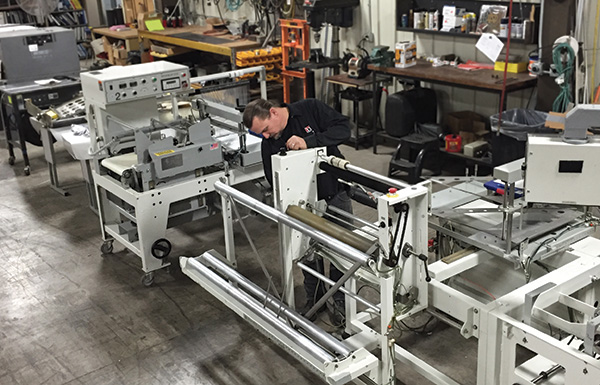
Training maintenance teams in these procedures is similarly crucial. Routine workshops and hands-on training sessions empower employees to perform repairs promptly and accurately. Moreover, promoting a society of constant enhancement motivates feedback from specialists, resulting in enhancements in repair service methods and procedures.
Advanced Diagnostic Tools

Advanced diagnostic tools provide comprehensive understandings right into the problem of product packaging equipment. For circumstances, thermal imaging cameras can identify overheating parts, permitting timely intervention. Vibration analyzers keep track of machinery vibrations, identifying variances that might suggest mechanical mistakes, while ultrasonic detectors can identify air leaks or electrical discharges that are not noticeable to the nude eye. These tools collectively add to a much more exact and informed upkeep method.
Furthermore, integrating innovative diagnostic devices into maintenance protocols enables data-driven decision-making. The gathered data help in forecasting devices failures and intending targeted Visit Website fixings. Businesses can designate sources much more efficiently, reduce upkeep expenses, and boost the total reliability of their packaging systems.
Training and Ability Advancement
The performance of sophisticated analysis devices is considerably improved when combined with thorough training and ability growth for maintenance personnel. Training programs tailored to the particular requirements of product packaging devices are crucial.
Skill development initiatives can take various types, including workshops, accreditation programs, on-the-job training, and cross-training among employee. Stressing continuous understanding ensures that professionals are abreast of the current technical advancements and upkeep techniques. Additionally, investing in skill development fosters a society of innovation and problem-solving, enabling upkeep teams to attend to devices issues proactively.
Moreover, trained employees add to lessening downtime and enhancing devices performance, inevitably bring about boosted operational performance and expense savings. Establishing a structured training plan, lined up with business goals, ensures that the labor force is competent and certain in preserving high standards of tools care. This strategic strategy to training and skill development is crucial in accomplishing streamlined upkeep operations in the product packaging industry.
Leveraging IoT and Automation
In today's swiftly developing product packaging market, IoT and automation are changing maintenance methods, supplying unprecedented degrees of performance and accuracy. By incorporating IoT-enabled sensing units and devices, packaging tools can currently communicate real-time information regarding operational standing and potential faults. This connectivity permits predictive maintenance, where issues are recognized and dealt with prior to they rise right into costly break downs, therefore minimizing downtime and prolonging tools life-span.
Automation more enhances these capabilities by automating routine maintenance jobs and diagnostics. With the implementation of automated systems, companies can improve their maintenance routines, minimizing hand-operated treatment and the margin for human error. Automated informs and reports created by IoT devices ensure maintenance teams are always educated, promoting an aggressive technique to devices care.
In addition, the combination of IoT and automation facilitates seamless information evaluation, allowing better decision-making processes. By taking advantage of data analytics, organizations can acquire insights into equipment performance trends, maximize source allowance, and enhance general operational efficiency. This technological harmony not just decreases maintenance costs yet additionally improves efficiency and reliability in packaging procedures. As the market continues to advance, leveraging i thought about this IoT and automation is crucial for maintaining an one-upmanship in devices maintenance.
Conclusion
The assimilation of predictive upkeep techniques, effective repair work procedures, and progressed analysis devices substantially boosts packaging equipment maintenance and repair service solutions. This thorough method not just expands the lifespan of equipment but likewise increases efficiency and dependability, inevitably optimizing functional performance in product packaging procedures.
In the world of product packaging devices maintenance, predictive maintenance techniques have like it emerged as a transformative approach to reducing downtime and enhancing operational effectiveness.Using sophisticated diagnostic tools is critical in improving the maintenance and repair service of product packaging devices. In addition, investing in skill development cultivates a society of innovation and problem-solving, making it possible for upkeep groups to attend to equipment problems proactively.
Automated reports and signals generated by IoT devices guarantee upkeep groups are constantly informed, advertising a proactive strategy to devices care.
The integration of anticipating upkeep strategies, effective repair service procedures, and progressed analysis tools significantly improves packaging tools maintenance and repair solutions.